In recent years, the rapid improvement of new energy battery performance has driven the rapid development of the new energy industry. The rapid development of new energy battery applications has put forward higher, newer, and more stringent requirements for battery performance, and battery R&D and production must be continuously improved to adapt to the new market environment.
New energy battery cell cleaning is a new process to meet the new application requirements. Compared with the existing laser lug cutting method, it can significantly improve the space utilization of the battery and make it have higher energy density; on the other hand, the laser cleaning coating method can be used for continuous and uniform coating in the pre-process, which can improve the uniformity of the cell compared with the unstable control of the surface density in the gap coating method. In addition, the poles’ uniformity and the equipment’s stability can further improve the charging and discharging performance of the battery.
As we all know, when it comes to laser cleaning, it is impossible to avoid the cleaning threshold and damage threshold of the material; we use the process parameters for the cleaning of the pole piece coating just needs to be between the cleaning threshold and the damage threshold of the material. The damage threshold is an inherent parameter related to the laser and material, generally obtained through experimentation.
The principle of damage threshold calculation.
As shown in Figure 3, the light intensity distribution of a Gaussian beam is plotted between the energy density and the radius of the cross-section as
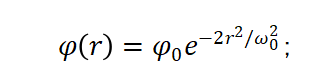
Where r is the distance to the center of the beam; φ0 is the energy density of the laser beam; ω0 is the beam waist radius. Therefore, the single pulse energy of the laser can be expressed as:
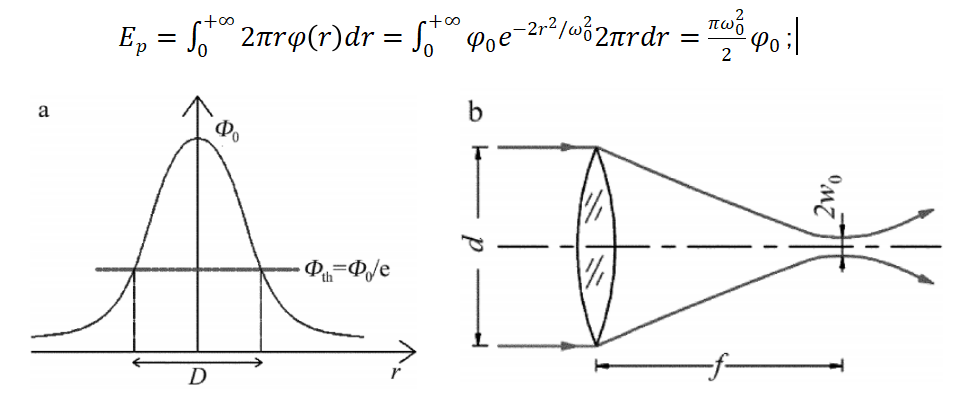
That is, the relationship between the central energy density and the pulse energy is:

The relationship between laser single pulse energy and average power (p) and frequency (f) is:
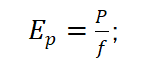
So:

Let φth be the energy density of the outer contour when the material is damaged in the area of diameter D. Φth is the boundary energy at which the laser can damage the material, that is, the damage threshold of the material.
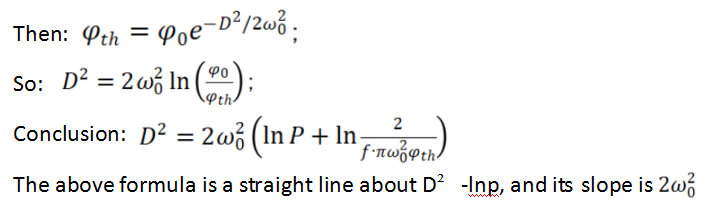
Therefore, according to the definition of the material damage threshold, the energy density value when the laser damage diameter is zero is the single-pulse damage threshold for laser interaction with the material. Therefore, experimentally obtained by the material’s single pulse damage diameter and the corresponding data of the laser power, through the linear fitting, can be deduced from the material’s single-pulse damage threshold.
However, in the actual laser cleaning process, we more often use the spot lap in the form of multiple pulses for surface removal. So you also need to set different power energy densities and the number of pulses, the measurement of its damage to the material aperture, through the linear fit to derive the number of pulses under the material damage threshold.
We used this method to test the damage threshold of anode copper and cathode aluminum foil with multiple pulses based on the material damage threshold calculation principle. We found that the foil will not be damaged under the value below, which meets the new energy lithium battery use requirements.